What kind of advancement does Die manufacturing Rajkot professionals offers?
- novelmouldcom
- Jan 19, 2021
- 3 min read
Die casting is a broadly utilized method to modestly make metallic parts for an assortment of utilizations. The cycle of die casting has been being used for many years by die manufacturing Rajkot, yet developments in procedures and materials have improved the proficiency of the cycle and the nature of the eventual outcome.
Die casting by emptying liquid metal into a die, otherwise called the gravity pressure technique, is an assembling strategy that has been utilized for many years. Advancements in the die casting cycle prompted a blast of die casting for some applications in the mid-1900s, especially when zinc and aluminum amalgams turned out to be more promptly accessible.
Pressure Injection Die-Casting
Quite possibly the main advancements in the die casting cycle were the improvement of the pressure injection measure. One of the soonest pressure techniques was squeeze casting, which included putting a metal part that had been warmed into a shape and applying pressure by leverage. The squeeze casting strategy was first utilized for assembling hatchet heads. However, this technique was restricted to leaves behind exceptionally straightforward shapes. Utilizing pressure permitted the liquid metal to be constrained into all bits of the shape, bringing about the capacity to die-cast more unpredictable parts with a better surface completion.
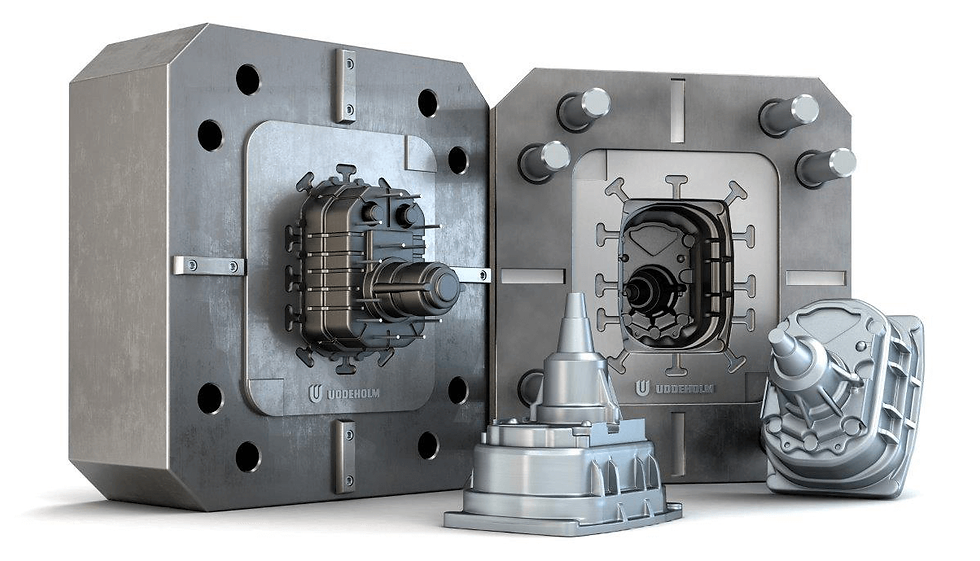
Advancements in Materials for Die-Casting
Early die casting cycles utilized lead or tin amalgams since they could be effortlessly liquefied and dealt with. The liquefying purposes of these amalgams were adequately low to avoid harm to the die. The improvement of more tough steel composites for molds and tooling took into consideration compounds with higher liquefying temperatures to be utilized. During World War I, new zinc and aluminum amalgams were presented, and the utilization of tin and lean declined quickly. Magnesium and copper combinations likewise came into utilization in the primary portion of the twentieth century, giving manufacturers’ adaptability in their design and material decisions.
Die-Casting and Computers:
After the advancement of pressure, infusion die casting and the presentation of new composites, the die casting cycle remained genuinely steady for a long time until the acquaintance of the PC with the assembling business. PCs are presently utilized all through the manufacturer and design measure:
I. Mold Design: Digital plan frameworks permit specialists to make and assess form plans electronically, bringing about less models and plan emphases.
II. Mold Fabrication: Computer-aided manufacturing cycles and advances in tooling take into consideration extremely complex bites the dust to be made with insignificant human work. Complex bends and complicated details can be machined into the form with a CAM application regulator.
III. Process Automation: Computer frameworks can handle the genuine die casting cycle and screen the status of the part during all segments of the assembling cycle. Frameworks can keep up the right pressure during casting, screen the temperature of the liquid metal and the shape after casting, control part cooling through water channels, and decide when the part can be extricated from the form.
Despite the fact that the general idea of die casting has not changed fundamentally in the last many hundred years, advances in cycle, materials, and innovation have permitted makers to build better and more mind-boggling casts and parts in a practical manner.
Significance of Having the Right Die Manufacturing Rajkot
The best die casting makers have a method of directing what's best for an organization and their creation necessities. They understand what's correct, what materials to utilize, and will naturally think about the overabundance of details that the organization will need for their items. These producers have a method of fitting services, particularly for their clients, and understanding what will cause the clients glad and not consume their pockets so a lot.
Experienced die manufacturing Rajkot Professionals of Novel Mould know the significance of time and how an item's prosperity may need to rely exceptionally upon the time delivered and accessibility of it on the lookout. They know how long they have and won't waste on any expense, regardless of whether there are unavoidable occasions or mishaps that may occur all through the cycle, a decent producer will have a back-up arrangement to keep the creation cycle going at the correct speed without trading off the nature of the item and completed thing. The ideal manufacturing services for your organization will change by experience, cost and bundles, time, and the die-cast measures they can give.
Comments